
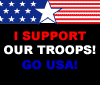

Help keep
FORDification.com
banner-free!
|
|
1967
Assembly Plant Paint Booth Gallery |
|
|
 |
Webmaster's Note:
The pictures on this page were posted to Facebook in
September 2018 by Marlon Reid and are hosted here with his
permission. His father Ross Reid was a University of
Waterloo engineering student and these are his pictures. As
a student, they rotated him through all areas of the
assembly plant to give him a well-rounded experience. Though
Ross worked in other areas besides paint, these are the only
pictures he took during his time there. Marlon sat down with
his father and 'interviewed' him for the following article. |
|
My Dad’s Ford
Experiences
I worked at the Ford plant
in Oakville, Ontario for 2 work terms from the University of
Waterloo where I was a Mechanical Engineering student in the
Co-Op program.

Fig. 01 |
My first work
term was in 1967, during which I worked on the
production line and tried to work on
optimization and improvements, most of which
were intended to reduce rework or failed
inspections.
In 1968, I
worked in the paint and body line where I was
made responsible for quality control.
The plant made
both cars and the F-series truck and employed
7000 people, with 2500 being on the truck line.
The plant was virtually brand new and 1967 state
of the art when I worked there. It was a pretty
huge set of buildings and was quite fun riding
around on my bicycle. |
Q: Did you ever see
any emergencies or injuries?
A: No, no actual injuries or serious accidents. A few
near-misses. There were panic buttons on every column and
that would shut the line down. It was a last resort though
and if someone pressed it, chances are the disaster would
have already happened. I never saw it though. Each guy at
his position had less than 2 minutes per vehicle to complete
his specific task. They were turning out 33 units (finished
trucks) per hour. I saw things like air tool lines getting
caught in the chain drive that moved the line forward. Say
for example a guy on the chassis line was riveting
structural members on the chassis and his hose slumped into
the chain. There’d be yelling “hose caught, hose caught!”
None of the other guys could help, and a supervisor would
come running with a new air hose and tool, the caught one
would just go and get sucked up and destroyed. Sometimes the
guy could get the tool off the hose and just lose the hose
back to the manifold, but you get the idea. Stopping the
line for such an incident was not done.
|
Q: What type of optimization would a student be involved
in?
A: Well, lots of things. They wanted us to understand
the whole line, so it was good thorough experience. But what
the hell did I know? I was a 22 year old kid. A lot of the
time, it was small stuff. For example, they would set the
toe-in at a specific machine, but by the time the steering
wheel and column were installed, the chassis had been
flipped a few times, things had moved, etc. The steering
might have moved a bit and so when the column was installed,
the steering wheel would not be straight relative to the
wheels themselves. Eventually, I recommended adding a step
to the toe-in, which was painting an alignment mark when the
wheels were straight. I’d do other motion studies and come
up with things like changing the sequences slightly to save
on actual body movements etc. We were always trying to claw
seconds out of the timeline. I was always a pain in the ass
with my clipboards. One time when I wasn’t looking, someone
put a capacitor on my clipboard. I didn’t see who did it,
but I wondered if it might be charged. Nobody was looking,
where did it come from? I thought it would be like picking
up a knife, one just has to do it safely. So, I carefully
picked it up and man, that thing bit me in the ass so fast.
Bam! Big shock. Everyone laughing.
During this Toe-in study,
I was responsible for driving those trucks off the line and
out into a test track. I was the first person to drive a lot
of trucks. I’ll tell you, some of them didn’t start first
try!
Q: How long did it
take to make a truck?
A: We were making 33 per hour, which was our target.
Each truck from the first step of bucking to completion took
about 2 days to make it through the entire line.
|
Q: What else did you have to do?
A: I remember they had a wrecking yard out in
Hamilton. This was about 30 min away from the Oakville
plant. Any parts or vehicles that were not up to snuff were
sent there to be destroyed. Say for example a truck were to
fall during loading of a train, or just have too much damage
to repair, it would be destroyed. They didn’t want it to
make its way to market and impact Ford’s reputation or
worse, be a safety liability. The same was true of parts
that were deemed not up to snuff. My name came up and it was
my turn to go to this scrapper and witness the destruction.
So, I took one of the cars and followed this truck of stuff
out. I had a clipboard, itemized to the load and was
supposed to sign off. I learned that this was because they
were fearful of a black market in defective parts passing
through the wrecker’s hands. The cars and trucks were easy
to wreck – put them in a machine and they get crushed
Goldfinger style and come out as a little cube. The parts
though – transmissions, rear ends, major sub-assemblies –
well they had to be individually destroyed on a big shear.
That was time consuming. The guys kept saying that I should
just sign and go enjoy an afternoon off, but I was young and
keen, so I watched it all, which did not seem to thrill
them. I was too naïve to realize that I was messing up their
scam.
I also had to participate
in the year-end changeover. Everyone would be sent on
vacation for 2 weeks and those that stayed would be
responsible for adjusting and stocking the line in their
absence. All the old parts and tools that didn’t apply to
the new model year were removed and replaced. This included
all the paint supplies, etc. 67 to 68 wasn’t a radical
change in body style, but there were enough things that we
had a lot to do. Maybe the truck fans you told me about can
figure out what they were, it’s been a while.
|
Q: How about the paint line?
A: The paint line was my second term. As you know,
I’m colour blind, but what the hell. They had 12 standard
colours and then non-standard colours and also special
colours. All told, the guys were painting something like 24
different colours. [Marlon’s note: I will annotate some of
the photos to show you what he meant]. I was responsible for
quality control. It got to where if I saw a truck out in
town, I could tell who had built it by the way the caulking
was daubed on. Each guy had his own signature like a
wireless operator in WWII.
The white bumpers,
mirrors, grilles and rims were painted at the car plant
across the alley.
|
There were 12 guys to paint a truck. They worked on opposite
sides, painting up to the centerline. The best painters were
at the end of the process. The colour code would be written
on the firewall early in the build with a bleedable grease
pencil. That way the painters could see it coming down the
line and get ready without reading the build sheet itself.
[Marlon’s note: his 1967 report deals with how the build
sheets are made, how the VIN plates and ID tags are made and
associated with each vehicle, when they’re installed, etc].
The bleedable pencil would show up through the primer. They
used the same guns for every colour, just would switch and
run the new colour through it for a few seconds before
applying it to the truck.
The most hated job was
being in “the pit”. It wasn’t called a punishment position,
but it really was. If someone had been late a few times or
screwed up, they’d get rotated to that job. They had to go
in a pit like it sounds under the line and paint the primer
on the underside parts of everything as it came over top.
Miserable hazy, awful.
I was responsible for
quality at different levels and was moved around so I could
see what it took to do a good job. The guys would say, “oh,
you think it’s so easy, why don’t you take a try?”, and hand
me the gun.
|
Q: Did you paint some trucks?
A: Yeah, I screwed up a few units.
It was interesting how quality would slip as
the day went on and quotas would be in danger. It really is
true that you want your vehicle built around 2 p.m. on
Tuesday. Definitely not late in the day on Friday. Guys
would be begging inspectors to pass their stuff, promising
to send them out to dinner on them, etc. They’d also sneak
the speed on the line a little faster to try and make up for
any slippage. It was a constant battle between the union and
the management over that issue.
There was inspection at every step, and
they’d assign extra inspection to units that they knew had
been purchased by employees. The build sheet would be
specially marked and nobody would cut any corners on one of
those units.
One time, I was inspecting on afternoon
shift [started late afternoon, went until late at night].
This was a bad shift because guys with drinking problems
would drink all day and then come to work drunk. One of our
painters was drunk this one day and his skills were down. He
was causing reject after reject and it was my job to send
him home, which was the right thing to do. However, it
wasn’t the “correct” thing to do. The contract with the
union was nearing renewal and negotiations were a little
tense. It turned out this guy was the job steward, and my
sending him home caused a mass walk off. That was the only
time I saw the line stop, actually. The bosses chased the
workers out into the parking lot and begged them to come
back. The actual “correct” answer would have been to send
him off to some flunky job like counting inventory where he
couldn’t hurt anything, just to keep the union happy. I
didn’t know that at the time though.
|
Q: What did you do with the rejects?
A: They were sent for repair by diverting them down
the tu-tone line where more paint was to be applied anyway.
If they failed after that, there was a 3rd chance for paint
repairs with air-cured paints, but that was an inferior
product compared to baked enamel of the main line and was
not desirable.
Q: What type of inspections were
there?
A: Runs or sags and the opposite – inadequate
coverage. Debris in paint. Adhesion.
Q: How did you test adhesion?
A: that was done on completed vehicles. They’d go out
to the parking lot and in a low profile place, like below
the hinge in the door jamb, they’d take a boxcutter knife
and scratch a grid. They’d put tape over that grid and pull
it away. If they couldn’t pull up any squares, it was good
adhesion.
Q: What if they failed at that
point?
A: Hmm, I don’t know!
That’s about all I have from my dad. He was tickled that you
guys liked his photos so much. I remember that as a student
ostensibly in a management role, he had a labcoat (not
coveralls) and his pants and shoes were glazed by the end of
a workterm. He tried to wear the same pants every day to
avoid wrecking extra clothes. They were hard and shiny from
the knees down. I wish he'd saved those, it would be neat to
see. I have his reports too, which
are the kind of dry reading you’d expect from an engineering
student, but also pretty interesting.
|
|
|
 |

Want to link to
this site? Please save this banner to your hard drive to place on your
webpage.
The correct link to use is
http://www.fordification.com
|