KINGPIN REMOVAL
If you're planning on
dropping off the axles, kingpins and spindles off at the machine shop
(the recommended route),
you can skip ahead to the Reassembly &
Reinstallation section right now. However, if you're a masochist
and want to save the money and do this all yourself, keep reading on....
So...you're going to tackle the job of kingpin removal and replacement
on your own. Well, be prepared to use a BIG hammer (aka BFH) and lots of heat (and
more than a few loud four-letter words!) if you (or the previous owner) neglected to keep his front end properly
lubed.
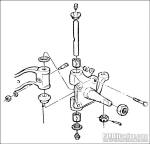
Fig. 1 - The kingpin bushings are located
in the spindle only.
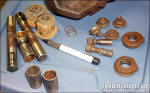
Fig. 2 - Here are all the old
front-end parts: kingpins and retaining pins and bushings, axle
pivot bushings, grease caps and shims.
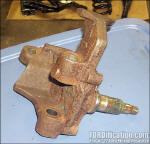
Fig. 3 - Here's the freshly removed spindle.
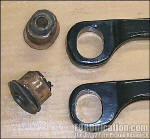
Fig. 4 - Be sure to replace
the axle pivot bushings while everything's easily accessible. |
Start off by cleaning the whole kingpin region as much as possible, and
then start by removing the kingpin's tapered locking pin. You'll remove
a nut and then drive the pin out of the I-beam. Then remove the top and
bottom grease caps to expose the ends of the kingpin. Wipe as much of
the old grease out as possible. Since the kingpin
is just a straight pin, it can either be driven out the top or the
bottom. Be sure to wear safety glasses, as the kingpin is a hardened
steel shaft and therefore brittle, and it's always possible for a
misaligned hit to cause a chip to go flying.
If the front end was properly lubricated during it's life, the
kingpin should come out fairly easily after the first couple of good
hard whacks, but most people say that it takes a lot of pounding to get
them moving. Once they do start moving it usually gets a little easier.
The use of a brass drift with a slightly smaller outside diameter than
the kingpin is highly recommended. Using a steel drift can also booger
up the threads in the spindle necessary for securing the end caps. Just
be careful to not mushroom the end of the kingpin, as further removal
will be next to impossible! One nifty trick is to remove the upper
grease cap and drill a 1/2" hole in the center of it, and then
reinstall. You can then use a 1/2" drift to drive out the kingpin, with
the grease cap acting as a guide to keep things centered and to protect
the grease cap's threads in the spindle. And don't worry...your kingpin
set comes with new grease caps.
If your kingpins don't budge at first, you can start applying heat to the axle
(not the spindle), being careful not to get it cherry-hot which could
affect the temper of the steel, and attempt to drive the kingpin out
using your BFH. You might find you'll have to break out the Liquid Wrench
or PB Blaster and soak the heck out of everything and just let it set for a day or so before trying
it again.
Once the kingpins are out, start by cleaning up the kingpin bore
in the axle using some emery cloth. (Do NOT use a brake hone!) Don't get
carried away here...you just want to clean it up. Once you can lightly
tap the kingpin into this hole with just a little resistance, stop!
Repeat this process with the spindles' kingpin bores.
Now you're ready to install the kingpin bushings. If you're using the
plastic bushings, you should be able to tap them into the spindle using
a block of wood. The bronze bushings will need to be pressed in and
reamed to fit the kingpin and is a job best left for the machine shop. A
brake hone will not get the job done, as the upper and lower bushings
need to be done together at the same time. This is a fast and cheap job
that you shouldn't attempt yourself without the proper equipment.
Next, you need to
replace the axle pivot bushings. These are pressed into the axle but can
be done at home if you have access to a hydraulic press. Considering how
very cheap the bushings are, replacing them should be done regardless of the old bushing's
condition. Might as well do it now while it's easy access, right? I
replaced my stock rubber bushings with PST's polygraphite bushings which
required the use of the original outer shells. Since the machine shop
messed up the shells of the original bushings when they were being
removed, and considering new bushings were extremely inexpensive, I
opted for buying a new set and drilling out the rubber portion and then
just pressed the new shells back into the I-beam.
Once the kingpin bushings are pressed in and reamed and the axle pivot
bushings are installed, you can begin the actual reassembly...

|